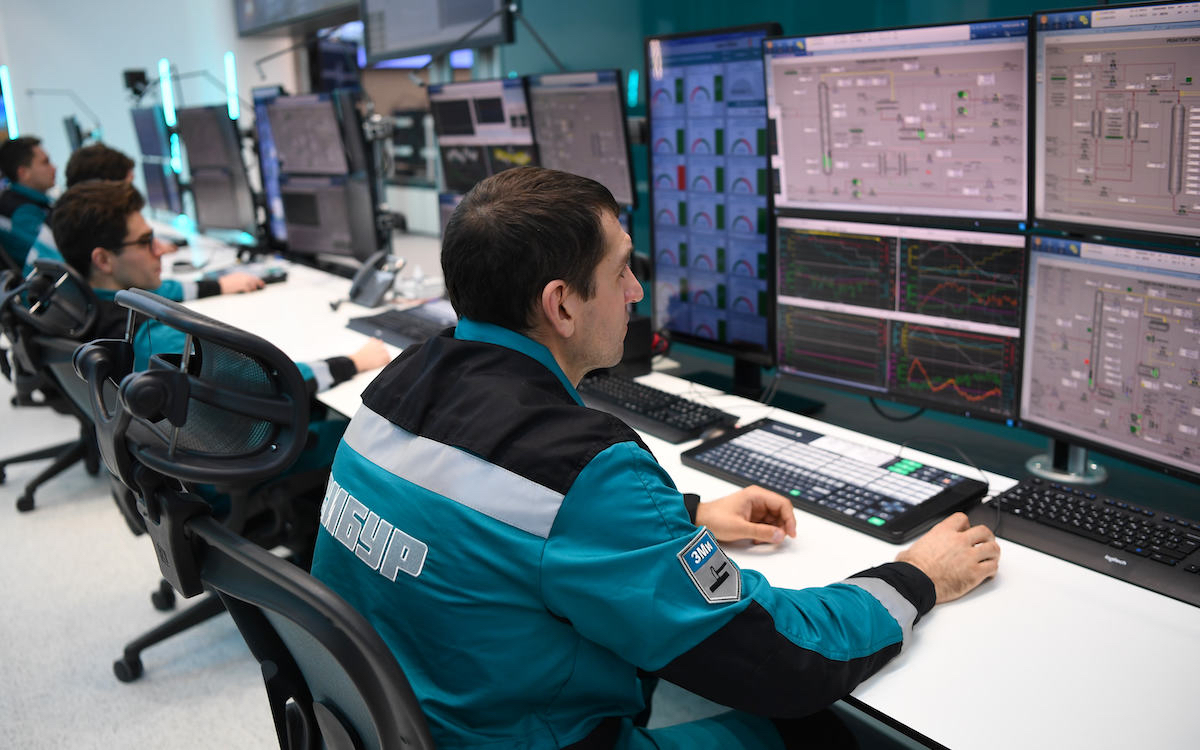
Поломки и неисправность оборудования составляют 42% незапланированных расходов компаний. Еще в 2014 году в Американском обществе качества провели опрос компаний и выяснили, что 82% предприятий, цифровизировавших свое производство, увеличили эффективность, 49% сократили количество бракованной продукции, а 45% повысили удовлетворенность клиентов. Сегодня технологии могут гораздо больше. На примере завода «ЗапСибНефтехим» нефтехимической компании «Сибур» рассказываем, на что способен интернет вещей и как он улучшает производственный процесс.
Современное производство: зачем заводу «интернет вещей»
Управление процессами с помощью машин — это осознанный подход к контролю производства. Компания «Сибур» установила систему «Эконс» на 34 производствах своих ключевых предприятий, а с начала нового года ее начнут использовать все площадки компании.
«Эконс» — это система визуализации, которая поддерживает оптимальный режим технологического процесса. Система учитывает параметры, которые важны для работы конкретной секции. Рассчитывая их, она переводит все производственные показатели в денежный эквивалент и выводит на экран текущую ситуацию на установке в виде спидометров с зеленой и красной зоной.
«Зеленой» зоной на заводе называют норму. Это диапазон, в котором оборудование работает с максимальной эффективностью и обеспечивает лучшее качество.
«Умные» системы: как технологии помогают контролировать производство
«Умный» завод «ЗапСибНефтехим» построили всего за четыре года. Запускали его в разгар пандемии, когда зарубежные специалисты, курирующие строительство, не могли приехать. С многими партнерами взаимодействовали удаленно. Для этого члены команды завода надевали очки дополненной реальности, а их зарубежные коллеги, подключаясь к системе, контролировали сложные процессы, подсказывали, как настроить оборудование.
Очки дополненной реальности по-прежнему используют на заводе. Сейчас инструмент называют «удаленный эксперт»: благодаря ему сотрудники могут общаться и получать консультации от более компетентных коллег без передвижений, отнимающих много рабочего времени.
Промышленные предприятия накапливают огромное количество данных. Их собирают различные производственные системы, в том числе датчики интернета вещей. Далее они поступают в центр удаленного мониторинга в Москве, специалисты которого могут контролировать уже шесть производственных площадок с помощью предиктивной и вибродиагностики.
Начальник смены и операторы технологических установок работают в едином центре управления. Для контроля работы смен используются цифровые доски эффективности — дашборды с визуализацией задач, статусов, команд. Раньше руководитель вел параллельно около 20 разных журналов, куда записывал все, что происходит в течение дня.
Работу оборудования контролируют тоже с помощью технологий. На каждой установке есть своя NFC-метка: сотрудник прикладывает к ней взрывозащищенный смартфон, получает данные об оборудовании и фиксирует объект в маршруте обхода. До этого мониторинг оборудования фиксировался на бумаге.
Сначала персонал скептически относился к внедрению новых инструментов. При этом регулярный сбор обратной связи в процессе разработки продукта и взаимодействие с пользователями позволило сделать удобный инструмент, который прижился на производстве.
Выгодные технологии: как достичь экономической эффективности
Проанализировав весь цикл — производство, логистику, продажи, — в компании сопоставили свои показатели эффективности с показателями первого квартиля на мировом рынке, а затем разработали проекты, которые позволили сократить разницу и сделать каждый процесс более эффективным. Экономия — одно из основных преимуществ внедрения «умных» технологий в производственные и бизнес-процессы. Эффект от цифровых внедрений измеряется миллиардами рублей, горизонте нескольких лет цифровая трансформация принесет «Сибуру» дополнительные ₽60 млрд.