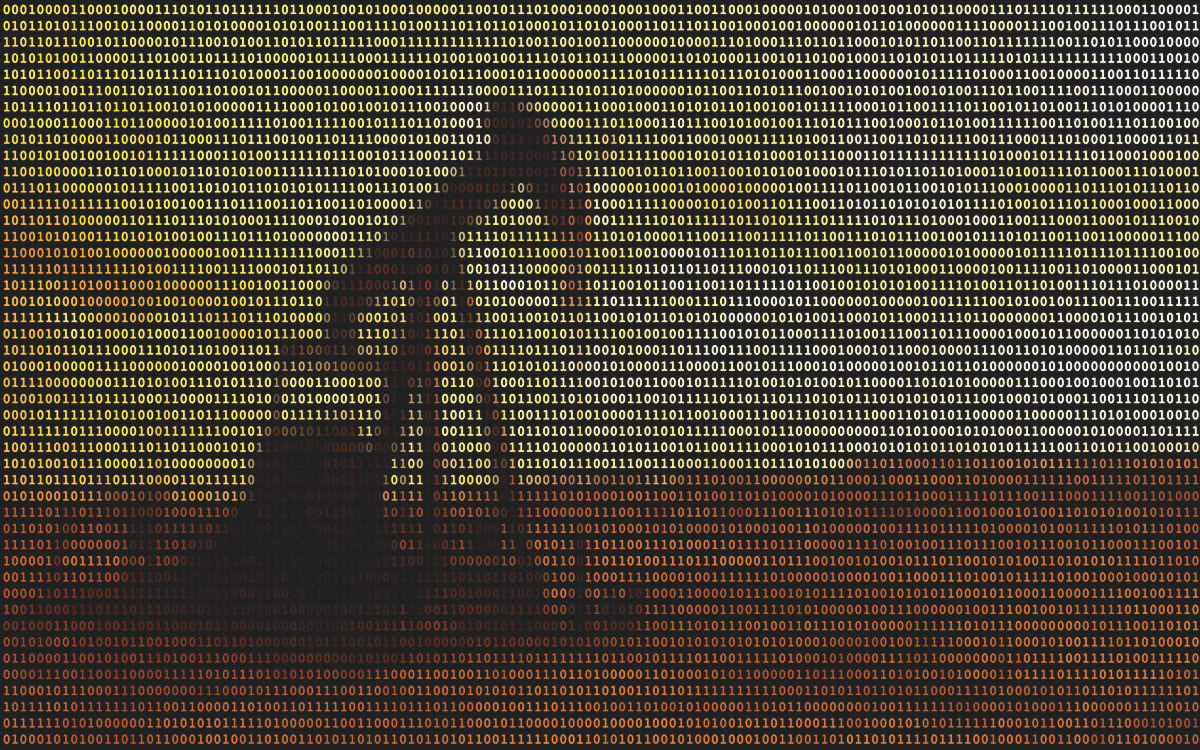
Для нефтегазовой отрасли двойники особенно важны по двум причинам:
- Многие объекты (нефтяные платформы и вышки) удалены от основного производства и головного офиса компании и находятся в труднодоступных местах. Поэтому виртуальные двойники помогают следить за их работой из любой точки, предпринимая поездки только в экстренных случаях.
- Добыча и переработка нефти связаны с повышенным риском, а аварии на объектах приводят к гигантским расходам и экологическим бедствиям. Двойники помогают избежать многих инцидентов, а значит — и расходов на ликвидацию последствий, простоев оборудования и человеческих жертв.
Для чего нужны цифровые двойники в геологоразведке
Цифровые двойники — это виртуальные модели отдельного оборудования или целых производств, которые помогают выявить уязвимости, спрогнозировать возможные сбои и повысить эффективность работы. В нефтяной промышленности их используют на всех этапах: от геологоразведки и добычи до нефтепереработки и трубопроводов.
Цифровые двойники собирают данные о работе оборудования и систем с помощью интернета вещей и рассчитывают вероятность износа или выхода из строя. Если показатели критические, система оповещает персонал, чтобы он принял меры. Также двойники помогают подобрать оптимальный режим работы, увеличить объемы добычи и нефтепереработки.
Как цифровые двойники помогают искать и добывать нефть
Цифровые двойники применяют в рамках концепции цифрового месторождения — оно же «умное» или «интеллектуальное». Изначально использовали умные скважины, оснащенные датчиками и системами для удаленного управления. Однако они не позволяли учесть геологические особенности месторождения и оборудования для добычи. Цифровые скважины помогают лучше контролировать процесс добычи и управлять им максимально эффективно.
Цифровой керн — это цифровые модели столбиков породы, которые извлекают из скважин в процессе геологоразведки, чтобы исследовать нефтеносный пласт. Извлечение и лабораторное исследование реальных кернов в лаборатории — сложный и дорогой процесс. Некоторые образцы разрушаются в ходе извлечения или испытаний, и тогда приходится добывать новые.
Цифровые керны помогают решить эту проблему. Для их создания образцы породы сканируют в томографе высокого разрешения, а затем проводят исследования на полученной 3D-модели. При этом на одном керне можно проводить неограниченное число экспериментов, не опасаясь повредить и разрушить его.
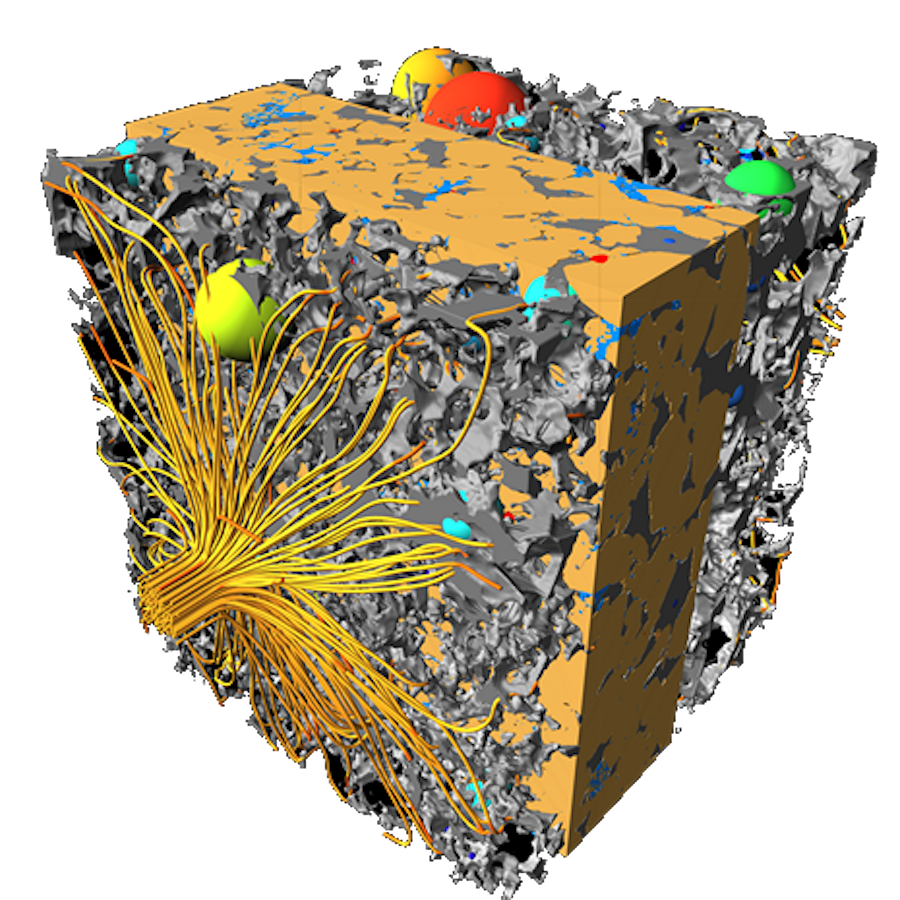
Цифровые двойники: кейсы нефтяных компаний
Shell
Нефтегазовая корпорация Shell, совместно со швейцарской Akselos (разработчик платформы для цифровых двойников) и датской LICengineering (консалтинговая компания в сфере морской энергетики) запустила двухлетнюю инициативу по созданию цифровых двойников для морских нефтедобывающих станций. Проект состоит из двух этапов:
- Разработка цифровой модели на основе выбранных параметров, которая позволила бы анализировать важнейшие показатели в рамках единой структуры.
- Объединение модели в единую сеть с датчиками, которые передают данные о нефтедобыче в режиме онлайн, чтобы прогнозировать работу всех вышек и предотвращать сбои.
Решение подключается ко всем целевым системам управления, включая сеть управления бурением, систему управления питанием и систему динамического позиционирования, которая помогает удерживать нефтяную платформу в заданной позиции. Данные собираются с помощью отдельных датчиков и систем управления на базе интернета вещей, анализируются с применением ИИ и машинного обучения и преобразуются в цифровые модели. Затем они передаются в реальном времени в Центр промышленной производительности и надежности GE для составления прогнозной аналитики.
Как ожидают в Shell, первая в мире цифровая буровая установка поможет снизить эксплуатационные расходы на оборудование на 20% и повысить эффективность бурения. Система уже помогла выявить множественные аномалии и предупредила о потенциальных сбоях за два месяца. Благодаря цифровому двойнику, персонал на судне и на берегу сможет получать целостное представление о состоянии нефтяной платформы и работе всего оборудования на борту в режиме реального времени.
BP
В BP с 2017 года используют виртуальные модели производственных систем на базе системы моделирования APEX. Благодаря решениям APEX за 2017 год мировая добыча нефти увеличилась на 30 тыс. баррелей.
Цифровые двойники помогают BP следить за нефтяными трубопроводами, скважинами и всей технической инфраструктурой в труднодоступных местах, в том числе в Северном море. С их помощью стало возможным строить цифровые модели любых объектов за 20 минут, хотя раньше это занимало до 30 часов. Они помогают тестировать различные сценарии в безопасном режиме, обнаруживать сбои и нарушения, настраивать скорость потока, давление и другие параметры, чтобы оптимизировать добычу и производство.
Eni
Итальянская нефтегазовая компания Eni использует цифровые решения на базе искусственного интеллекта и VR для моделирования операций, поддержки принятия решений и автоматизации буровых работ. Это позволяет имитировать анализ объектов в реальности и проводить расширенные тренировки по технике безопасности. Следующий шаг — разработка виртуального симулятора бурения.
Equinor
Норвежская компания Equinor с филиалами в 30 странах мира применяет цифровые двойники на месторождении Юхан Свердруп в Северном море, на которое приходится до 25% всей морской нефтедобычи в Норвегии. Данные о работе оборудования поступают в режиме реального времени и доступны через приложения на планшетах и смартфонах. Это позволяет решать сложные инженерные задачи и обеспечивать бесперебойную работу нефтедобывающих скважин.
«Газпром нефть»
В «Газпром нефти» с начала 2000-х годов реализуют решения для цифровых скважин, кернов и другие цифровые двойники. Они позволяют оценить объем и характеристики нефти и нефтепродуктов, планируемую нагрузку трубопроводов, прогнозировать состояние нефтеперерабатывающих установок, управлять инженерными данными и моделировать производственные процессы.
В 2017 году в «Газпромнефть-Хантос» (дочернее предприятие «Газпром нефти», занимающееся разработка месторождений в ХМАО-Югре) был запущен Центр управления добычей (ЦУД), объединивший все разработанные решения для более эффективной добычи нефти. Сегодня такие центры сопровождают разработку ключевых месторождений «Газпром нефти» по всей России. В среднем, в каждой добывающей дочерней компании «Газпром нефти» использует более 20 цифровых двойников во всех процессах нефтедобычи.
На этапе геологоразведки они помогают исследовать месторождения: находить и уточнять расположение пласта нефти, его характеристики и объем запасов. Ключевым проектом в этой области в 2020–2021 годах стало внедрение цифрового двойника сейсморазведки D-Seis. Инновационная платформа объединяет данные более 80 геологоразведочных проектов, а онлайн-сервис предоставляет удаленный доступ к статистике и аналитике специалистам по всей России.
На этапе добычи цифровые двойники, оперируя массивами больших данных в сотни терабайт, помогают выявлять возможные проблемы при эксплуатации скважин, участков трубопроводов и технологических установок, выдавая рекомендации по их решению. Модели машинного обучения помогают оптимизировать режимы работы оборудования. В Центре управления добычей «Газпромнефть-Хантос» данные с более 5 000 скважин поступают в цифровой двойник, на основе которого ИИ каждую минуту пересчитывает тысячи вариантов эксплуатации и выбирает лучший режим управления месторождением.
В 2020 году, в рамках комплексной трансформации блока разведки и добычи «Актив будущего», выгода от внедрения цифровых двойников превысила ₽2 млрд.