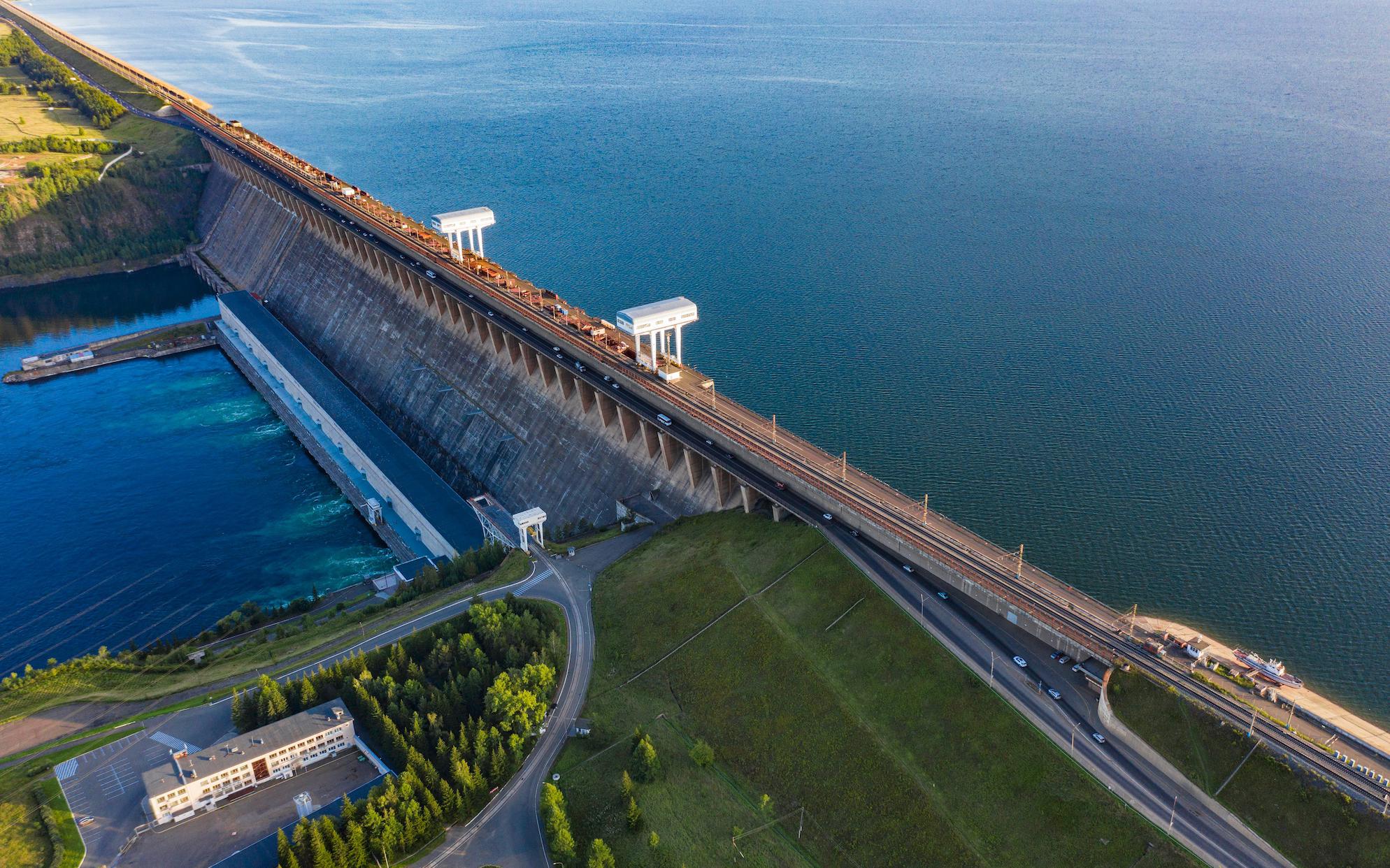
«Эн+» — вертикально интегрированный холдинг. В его состав входят два основных дивизиона — металлургический (объединенная компания «Русал») и энергетический (электрогенерация, угледобывающие предприятия). Также управляет активами в логистике и других отраслях.
Задачи
- Внедрить интеллектуальную систему, которая будет контролировать и прогнозировать техническое состояние оборудования на ГЭС.
- Снизить затраты на ремонт.
- Сократить потенциальный ущерб от аварий, связанных с поломками агрегатов.
Предпосылки и мотивация
У компании «Эн+» четыре крупных гидроэлектростанции — Братская, Красноярская, Усть-Илимская и Иркутская. Раньше основное оборудование на них ремонтировали по планово-предупредительной системе. Вид и периодичность ремонта зависели от требований, которые производитель указал в проектной документации.
Но это не единственный доступный сценарий. Планируя ремонт, можно отталкиваться не только от графика, но и от реального состояния агрегатов. «Есть мировая практика, когда ремонтные работы выполняют по техническому состоянию, при этом оборудование контролируют специализированные интеллектуальные системы», — рассказывает главный инженер гидрогенерирующего направления «Эн+» Юрий Дворянский.
В таких системах используют технологии предиктивной диагностики. Они отслеживают множество параметров и подают сигнал, если возникают критичные для агрегатов отклонения. Это помогает избежать крупных аварий и остановок оборудования, дает экономию и повышает надежность.
В 2019 году компания начала искать такую систему для своих ГЭС. Выбрали решение от одного из мировых лидеров, которое в конце 2021-го развернули на тестовой площадке — одном из гидроагрегатов Братской гидроэлектростанции.
Тестирование зарубежной системы прошло успешно — система могла спрогнозировать поломку агрегата за полтора месяца до того, как та стала возможной. Но в 2022 году производитель ПО ушел с российского рынка.
Решение
Основатель холдинга «Эн+» Олег Дерипаска (до 2018 года занимал пост президента компании) прогнозировал, что цифровая трансформация будет играть одну из ключевых ролей в развитии компании и, чтобы оставаться конкурентоспособными, необходимо обладать собственными компетенциями в этой области.
Поэтому к моменту ухода производителей зарубежного ПО холдинг уже располагал собственным инженерно-техническим центром, где были высококвалифицированные инженеры в сфере IT. Инженерно-технологический центр (РУСАЛ ИТЦ) создан в 2002 году в Красноярске и стал основной научно-технической базой компании. Наличие такой базы и компетенций позволяло развивать новую систему предиктивной диагностики собственными силами. Для этого выбрали платформу AggreGate SCADA/HMI из реестра отечественного ПО.
Василий Бердников, руководитель подразделения инженерно-технического центра «Русал» в Иркутске:
«Российская платформа, которая была в реестре ПО, — это некий конструктор, на базе которого можно строить свой продукт. Естественно, код надо было писать самим. Но самое главное — платформа уже обладала нужными алгоритмами, на которых строилась вся наша предиктивная диагностика».
Реализация
На создание собственного ПО ушло около семи месяцев. Сначала инженеры определили нормальное состояние оборудования. Для этого взяли данные за год со всех гидроагрегатов и выделили все режимы работы, при которых не было аварийных ситуаций.
В общей сложности проанализировали около 250 параметров — температуру, напряжение, силу тока, расстояние между элементами, расход жидкостей и т.д. «Они между собой связаны: меняется режим — меняется один параметр, другой, третий. Соответственно, все это надо отследить и смоделировать», — объясняет Василий Бердников.
Инженеры описали, как должны работать разные части агрегата и от каких показателей зависит их исправность. Все это объединили в диагностические правила. Для каждого параметра установили диапазон значений, соответствующий нормальному режиму. Как только значения выходят за верхние или нижние границы, система сигнализирует об этом.
Весь алгоритм разработали в «Эн+» с нуля, компания получила патент на изобретение.
Новую систему запустили на том же гидроагрегате Братской ГЭС, где использовали иностранный аналог. Оказалось, что собственное решение диагностирует параметры точнее, чем зарубежное.
За работой системы предиктивной диагностики постоянно следят специалисты компании. Группа мониторинга состоит из двух сотрудников. В случае сбоя они сообщают техническому руководителю станции о проблеме и вместе с главным инженером работают над ее устранением.
«Весь процесс мы контролируем, я могу зайти в приложение и посмотреть, как идут дела, задать вопросы, спросить, что делается для устранения дефектов, если система их выявила», — говорит главный инженер гидрогенерирующего направления «Эн+» Юрий Дворянский.
По его словам, решение постоянно эволюционирует. Например, в какой-то момент на одном из агрегатов сломался датчик, а система не отслеживала такие неисправности. В компании разработали и внедрили дополнительный алгоритм. Теперь ПО контролирует не только «железо», но и состояние датчиков.
К началу октября 2024 года предиктивную диагностику запустили на шести гидроагрегатах Братской ГЭС.
Юрий Дворянский:
«У каждого гидроагрегата свои параметры нормальной работы, каждый живет своей жизнью, поэтому просто взять и поставить систему нельзя. В течение двух месяцев мы ее обучаем под каждый гидроагрегат индивидуально. Первая, которую запустили в 2022 году, прекрасно работает до сих пор и нареканий не вызывает».
Результаты
С момента запуска с помощью системы предиктивной диагностики предотвратили 24 аварийные остановки гидроагрегатов. Проблемы заметили на ранних этапах и быстро провели ремонт, чтобы оборудование не вышло из строя.
Такие ремонты намного дешевле, чем замена сложных агрегатов при серьезных поломках. К тому же при незапланированной остановке компания может получить штраф на рынке мощности, подчеркивает Юрий Дворянский. Штраф за каждый день простоя — ₽2 млн. По оценке главного инженера, ремонт после крупной поломки длился бы минимум неделю.
Василий Бердников:
«Система предиктивной диагностики — это помощник для технического блока. Человек физически не способен каждые пять секунд анализировать 250 параметров и отлавливать, какой из них чуть-чуть отклонился от нормальных границ. И сейчас один человек с помощью системы контролирует работу всего парка основного оборудования».
В компании отмечают и другие эффекты от внедрения нового ПО:
- Более качественное моделирование прогнозных параметров — на 1–2% точнее, чем у зарубежного решения.
- Ниже затраты на приобретение лицензий и техническую поддержку.
- Проще дорабатывать и улучшать ПО, не нужно обращаться к дорогостоящим иностранным специалистам.
При этом сам продукт обошелся дешевле зарубежного. На подготовку и установку иностранного ПО направили около ₽30 млн. А создание собственного решения стоило ₽20 млн.
Реализация проекта на базе зарубежной системы оценивалась в ₽171,4 млн, включая ₽27 млн за НИОКР на пилотном гидроагрегате. На отечественной платформе проект стоит ₽84 млн, сюда входит НИОКР на пилотном агрегате (₽23 млн) и масштабирование на все 18 гидроагрегатов Братской ГЭС.
Планы и перспективы
До конца 2024 года систему предиктивной диагностики установят еще на шесть гидроагрегатов. Оставшиеся шесть оснастят в 2025 году, таким образом, решение заработает на всех 18 агрегатах Братской ГЭС.
Параллельно его планируют внедрять на Усть-Илимской ГЭС, там уже провели предпроектный анализ. «Пока не все гидроагрегаты на станции оснащены нужными датчиками, а чем больше оснащен гидроагрегат, тем точнее будет процесс выявления дефектов», — объясняет Василий Бердников.
В будущем технологию хотят запустить и на других ГЭС компании — Красноярской и Иркутской.
Инженеры также намерены создать «коробочную» версию решения. Она будет работать полностью автономно, не требуя платформы-конструктора или участия программиста.
В планах — запуск новых интеллектуальных инструментов на объектах компании. Например, диагностической платформы в виде собаки-робота. Ее оснастят тепловизорами и другими датчиками, чтобы отслеживать отклонения в работе трансформаторов, изоляторов и других приборов.
Василий Бердников:
«Робопес будет контролировать контактную часть, улавливать малейшие изменения параметров, буквально доли градусов. Человеческий мозг просто не в состоянии дать такой анализ. Все это нужно для повышения надежности. Мы находимся на стадии разработки техзадания, в 2025 году начнем внедрять роботов на ГЭС».
👀 Следите за телеграм-каналом «РБК Трендов» — будьте в курсе последних тенденций в науке, бизнесе, обществе и технологиях.