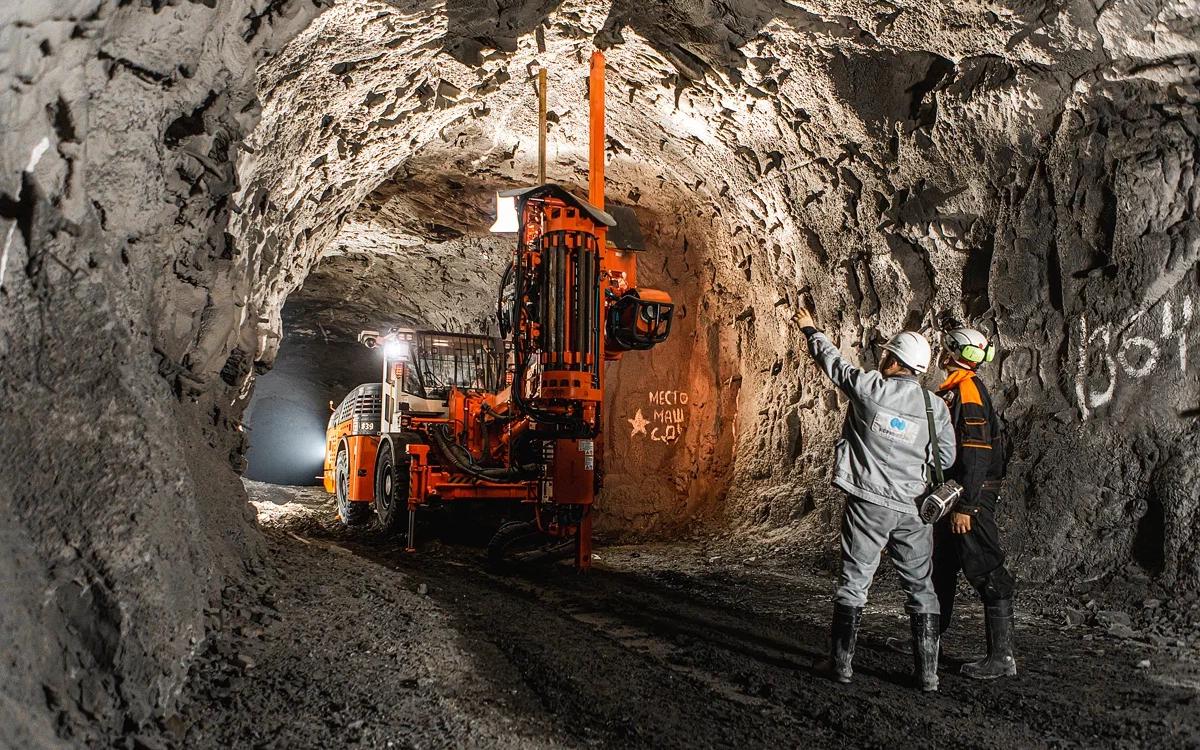
Об экспертах:
- Александр Рашковский, руководитель направления департамента технологических инноваций компании «Норникель». Создатель нескольких инновационных металлургических продуктов и центра исследований и разработок.
- Сергей Вагнер, руководитель направления по технологии рециркуляции.
Автоматизированная добыча
Один из главных трендов сегодня — человекоцентричность. Это очень долгосрочная тенденция, и она с нами не просто на ближайшие годы, а на целые десятилетия.
«Норникель» старается максимально снизить присутствие людей на опасных участках производства, используя различные механизмы. Во-первых, машинам легче выполнять работу, которая требует большой и монотонной физической нагрузки. Во-вторых, их можно поместить в опасные условия производства. Например, туда, где очень жарко, выделяются вредные вещества или существует угроза обвалов.
Уже сегодня в отрасли есть вектор в сторону полностью автоматизированных производств. К примеру, на обогатительных фабриках непосредственное участие человека в процессе минимально. Если вы сейчас зайдете в цех, то практически не увидите людей внутри, большая часть операций по настройке производственных процессов проводится удаленно.
В добывающем сегменте все несколько сложнее. Чтобы обходиться здесь без участия человека, нужно в первую очередь полностью автоматизировать процесс разведки полезных ископаемых. Мы должны точно знать, как в недрах расположены ценные ресурсы — медно-никелевая или, скажем, медно-золотая руда. Для этого надо увеличить объем разведывательных работ, в том числе бурения. И получить очень подробную 3D-модель разрабатываемого участка.
Сейчас большую роль в разведке играет экспертное мнение и накопленный опыт. На некоторых участках нужно жертвовать полезным ископаемым, ставя во главу угла безопасность работ, и решение об этом принимает человек. Но чем больше мы будем иметь точных данных о залегании полезных ископаемых, тем лучше мы продвинемся в сторону полной автоматизации. В частности, применение современных технологий искусственного интеллекта позволит создать автоматизированную экспертную систему, предсказывающую поведение объекта и повышающую эффективность добычи полезных ископаемых.
В части аналитики и составления пространственных моделей уже есть точечные решения. Более того, они активно применяются в промышленности. Но существуют и ограничения на применение этих решений, поскольку нельзя отбрасывать фактор законодательства. Вопрос учета разведданных и ископаемых, добытых новыми роботизированными способами, пока не до конца отрегулирован.
Потенциально первую зарегистрированную на государственном уровне схему полностью автоматизированной добычи мы получим через 20-25 лет. Но если снять ограничения, касающиеся учета, то это можно сделать намного быстрее — в течение 5-10 лет.
Новая образовательная парадигма
Автоматизация не значит, что мы уберем из отрасли всех людей. Просто человеку лучше находиться в теплом помещении и управлять оттуда роботами, чем стоять на краю угольного разреза и работать в условиях повышенного риска.
При этом количество людей в отрасли останется примерно тем же, что и сейчас. Возможно, в каких-то направлениях их станет больше, в каких-то — меньше. Но суммарная численность принципиально не поменяется.
Изменение способов работы приведет к формированию еще одного тренда — смене образовательной парадигмы. В будущем человек не только должен разбираться в своей непосредственной специальности и быть, допустим, хорошим маркшейдером или металлургом. Ему потребуется знать робототехнику и понимать, как себя ведет тот или иной механизм. Специалисты станут мультинаправленными. Казалось бы, далекие друг от друга профессии будут совмещаться.
Уже сейчас ряде инновационных образовательных программ металлурги учатся подходам к решению прикладных задач у специалистов ИТ, материаловеды ищут общие точки соприкосновения с биологами.
Пока невозможно точно предсказать, как будет выглядеть полный список востребованных специальностей в горной добыче и металлургии через 20 лет. У нас есть целый сегмент пока не существующих профессий — примерно 15-20% от общего числа инженерно-технических работников. Это белое пятно предстоит заполнять тем людям, которые еще не родились или еще не пошли в школу. Они поступят в институт только через 10-15 лет.
Но уже сегодня мы хорошо понимаем, что в отрасли складывается серьезный дефицит инженерных кадров. Средний возраст специалистов увеличивается. И как бы ни менялась отрасль, какие бы новации ни внедрялись, высокая потребность в инженерах вряд ли исчезнет. На любом этапе и при любой модели работы нужно понимать, как устроена металлургия и основные технологические процессы. Без этой базы мы не получим профессий будущего.
Выбросы как сырье для новых продуктов
Экологические метрики на наших глазах становятся одним из важнейших параметров проекта, в том числе и в металлургии. А разнообразные выбросы и отходы начинают рассматриваться как ресурс.
До недавнего времени техногенные отходы просто складировали. Но то, что раньше считалось загрязняющим веществом, теперь становится основой для новых материалов и продуктов. Сейчас мы серьезно рассматриваем целый портфель материалов и продуктов, которые можно создать внутри предприятия на основе экономики замкнутого цикла.
Например, все знают, что в руде содержится сера, а при производстве металлов выделяется сернистый газ. Его можно перерабатывать в серную кислоту или выделять из него серу. Но сера как таковая прямого применения в таких количествах не имеет. Тем более, производства расположены в Норильске и на Кольском полуострове, там просто некуда деть столько сырья. То есть для нас это условно бесполезный продукт.
Однако можно использовать серную кислоту — нейтрализовать ее с помощью известняка и получать гипс. А его, в свою очередь, применять в качестве закладочных смесей в нашем же производстве. Можно пойти еще дальше — из обычной серы сделать полимерную и использовать ее как пластификатор. Эта добавка нужна при производстве металлопластов.
С углекислым газом можно работать по похожей схеме. Уловив его и соединив с никелем, мы получим карбонат никеля, который применяется в литиевых батареях.
Производственные мощности на наших предприятиях обновляются достаточно часто. Мы меняем какие-то агрегаты, цеха, а от старых остается огромное количество металлолома. Его можно отправлять на переплавку, и на выходе получать стали и сплавы для строительства, новые полезные конструкции.
В «Норникеле» существуют только отдельные звенья полной цепочки замкнутого цикла, но мы развиваем это направление и создаем вторичное производство. Переработанные металлоконструкции, в том числе с высоким содержанием никеля, имеют большую потенциальную ценность. Никелевые сплавы широко распространены везде, где требуется жаростойкость. И в процессе такой вторичной переработки можно создавать материал, например, для газовых или самолетных турбин.
Рост эффективности и прибыльности
Новые технологии, которые мы только начинаем использовать, на старте всегда требуют инвестиций. Но в конечном счете с точки зрения прибыли компании не потеряют, а приобретут.
Вовлекая отходы в оборот, бизнес уменьшит свои затраты на покупные материалы. Предприятия будут шире использовать то, что у них и так есть. И производить из этого сырья товары — как для своих нужд, так и народного потребления.
Конечно, в моменте на многих направлениях вырастет инвестиционная часть, придется создавать какие-то новые модели работы и производства. Например, мощности по сортировке и сбору отходов — хабы, специальные центры, технопарки. Государство может участвовать в таких проектах в качестве партнера, предоставлять льготные налоговые режимы и другие послабления.
Кроме того, компании могут создавать партнерства, в которых реализуются схемы замкнутого цикла. В Дании уже несколько десятилетий действует Калуннборгский симбиоз. Промышленные предприятия обмениваются ресурсами — водой, энергией, материалами. Остатки или отходы одного производства становятся ресурсом для другого. Ежегодно участники проекта экономят примерно 24 млн евро, вовлекая во вторичное использование около 87 тыс. тонн материалов и 3,6 млн кубометров воды.
В перспективе масштабы экономии и вовлечения ресурсов многократно вырастут. Несуществующие пока производства сложно изменить нынешними метриками, но нет сомнений, что отдача будет огромной.
Период активного инвестирования составит примерно 10-–15 лет. Если мы начнем активно вкладываться в это направление прямо сейчас, то к 2035 году можем создать несколько десятков технопарков замкнутого цикла. А к 2050-му году они превратятся в самобытные производства, которые не только будут себя окупать, но и приносить хорошую прибыль компании.
Таким образом через 20–30 лет мы увидим практически полностью обновленную металлургическую отрасль — с высокой степенью автоматизации, с другим набором профессий и новыми уровнями экологичности и прибыльности. Но эти изменения не произойдут сами собой. Для этого потребуется комплексная работа с кадрами и современными технологиями, учитывающая накопленный опыт и возможности взаимодействия со смежными отраслями.